Analyzing the role of analytics in reverse logistics
July 26, 2022
Data analytics is a core focus for every business today. It is because the wealth of data when garnered adequately can bring exceptional business growth. From enabling cost reduction, seizing lucrative opportunities, and mitigating risks, to delivering customer-centric solutions, data analytics can help your business get to the top in no time. It is not just used for business functions, rather it can be used in all of them. In this blog, the focus is on the utilization of data analytics in supply chain management, particularly in the reverse logistics domain. Let's dive deeper into that.
Forward vs reverse logistics
It is important to establish an understanding that forward and reverse logistics are entirely different from one another. We are all aware of forward logistics, which is a straightforward process familiar to supply chain professionals such as: products flow from suppliers to production facilities or distributors, and then to retailers and customers.
On the other hand, reverse logistics runs backwards. It begins with the customer rather than the supplier, transitioning to the retailer, then to the distributor, and finally returning the products to the manufacturer or supplier in some cases. Reverse logistics can also include additional channels like recycling, refurbishing, or resale, depending on whether the supply chain is extended to the said processes.
How does reverse logistics work?
Reverse logistics recovers lost value from returned products or appropriately disposes of them. Annually, there is a significant volume of returned products worldwide, amounting to a trillion dollars. Consequently, to optimize these costs, supply chains of progressive businesses have implemented reverse logistics operations to maximize their value by recapturing it from returned goods.
Whether an organization has an in-house or outsourced reverse logistics facility, the process is the same. It starts with:
Return Processing:
It begins when a customer expresses disapproval of a delivered product and initiates a request to return the good. Typically, the customer contacts the seller's support centre or visits the online portal to report their discontent. Then, the support teams guide the customer to fill out a return form (not in some cases), which, upon authorization, triggers the return process.
The product is then retrieved from the customer and then forwarded to the retailer, distributor, or manufacturer, depending on the number of channels involved. The product's condition is evaluated by the teams concerned, and appropriate actions such as refunds, return shipments, or replacements are determined based on the evaluation.
Dealing with the returned goods
The returned product undergoes a comprehensive quality assurance process to assess its condition in real time. It is then categorized, as per the specifications of the supply chain and manufacturing facility, to determine whether it should be resold as new or returned or should it undergo recycling, refurbishing, or disposal.
Identify products for repair
An assessment takes place to determine whether the returned products can be repaired and promptly sent them to the repair department. These items can then be resold as new or used products.
Recycling
For any products that are beyond repair, reuse, or resale, ensure they are directly sent to recycling facilities.
Simplifying reverse logistics with advanced data analytics
The utilization of data analytics in reverse logistics has often been overlooked. However, organizations frequently come across challenges that are related to rising costs in the return management process, which can be complex and might require simplification to ensure speed and efficiency. This will lead to higher customer satisfaction. Here is an overview of some of the benefits data analytics offers in reverse logistics:
- A comprehensive view of potential outcomes by extracting and analyzing historical data of return requests.
- A remarkably accurate understanding of likely results based on past events with the customer profile and their interactions with the business.
- Anticipate actions necessary to avoid unfavourable outcomes while highlighting areas beneficial to the organization.
To enhance the performance of your warehouse operations, it's time you prioritize the improvement of your reverse logistics processes through data analytics.
Finally
The integration of data analytics into reverse logistics management is a groundbreaking concept that can revolutionize supply chain operations. By leveraging data analytics, businesses can enhance customer satisfaction, minimize costs, and increase profits. While implementing and integrating analytics can present challenges, our team of experts has a proven record of accomplishment in successfully transforming clients' supply chain operations through advanced analytics. We can provide a tailored solution for your reverse logistics needs. Connect with us to know more in this regard.
If you want to know more about digital selling and its solutions, please connect with our experts here to fast-forward your business growth through disruptive digital solutions.
Quick Link
You may like
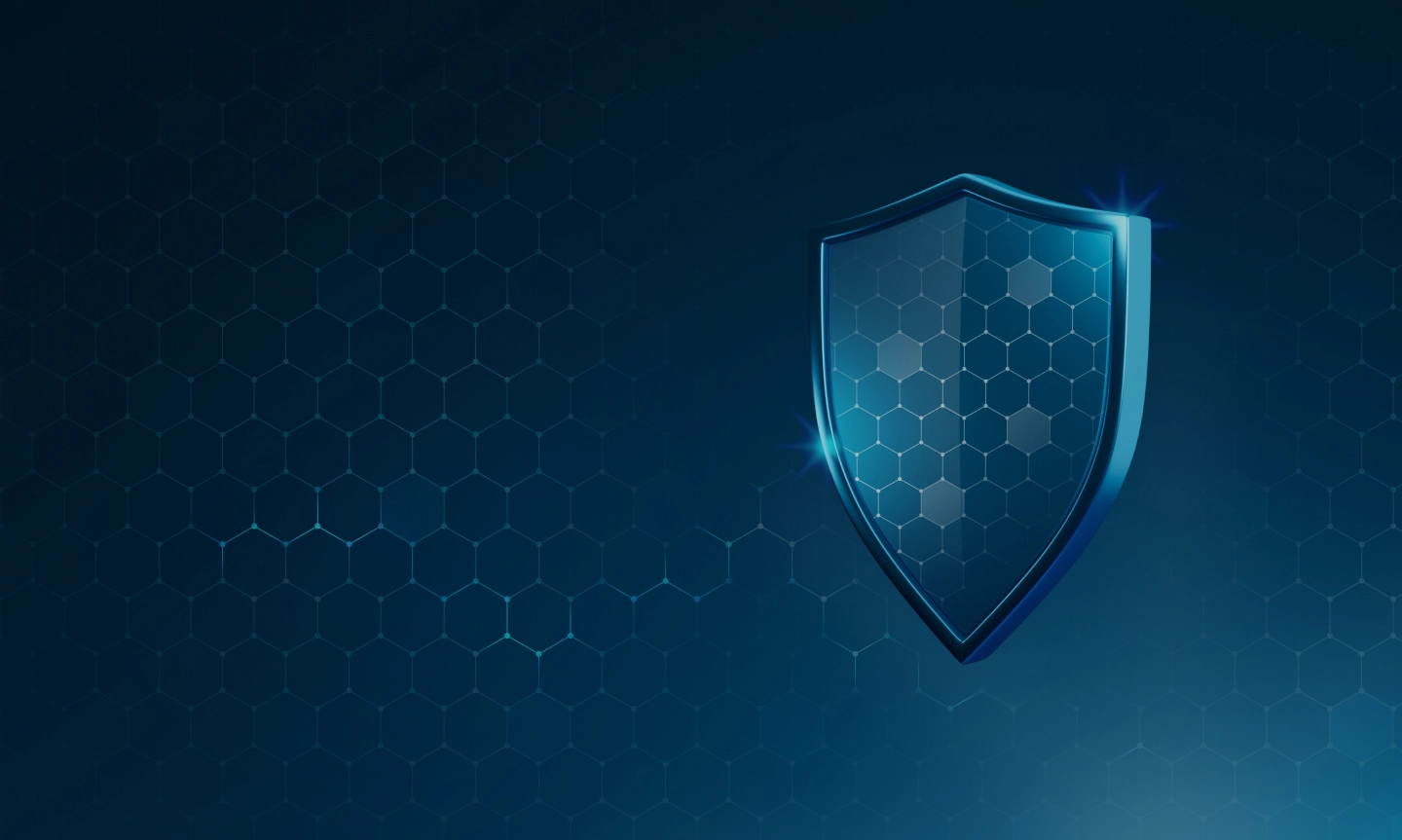
Critical infrastructure protection and its role in resilient enterprise cyber security
Critical infrastructure security as a robust business armor and how it helps you realize long-ter
READ MOREHow can we help you?
Are you ready to push boundaries and explore new frontiers of innovation?